donsrods
Well-known member
Tonight Dan and I went to the shop and while he was working on his Mustang, stripping all the sound deadening out of it, I worked on my firewall and trans hump some more.
I had to cut a hole in the drivers side of the firewall for the steering column to go through, and I was semi dreading that job, because I NEVER hit the exact hole size I need on the first shot. No matter how I measure I have always been off a little, but tonght for some reason I hit it dead on the first try !
Here is a picture of my column installed through the new hole.
Then I had to cut another hole in the new trans hump for the American Shifter to come through. Either I am getting better at it or something, but I also hit this hole in the perfect spot the first time too. I had to grind a little more out of the hole for the shift arm to move back and forth and on the other side for the neutral safety switch clearance, but it actually came out pretty dead on.
Here are some pictures of that hole and the shifter installed.
This week I am going to order a 4 x 10 foot sheet of 18 gauge sheet metal so I can finish up the floor and also start to bend up the bed. Next weekend I will get Dan to weld up all the tinwork so it is a permanent part of the subframe.
Don
I had to cut a hole in the drivers side of the firewall for the steering column to go through, and I was semi dreading that job, because I NEVER hit the exact hole size I need on the first shot. No matter how I measure I have always been off a little, but tonght for some reason I hit it dead on the first try !
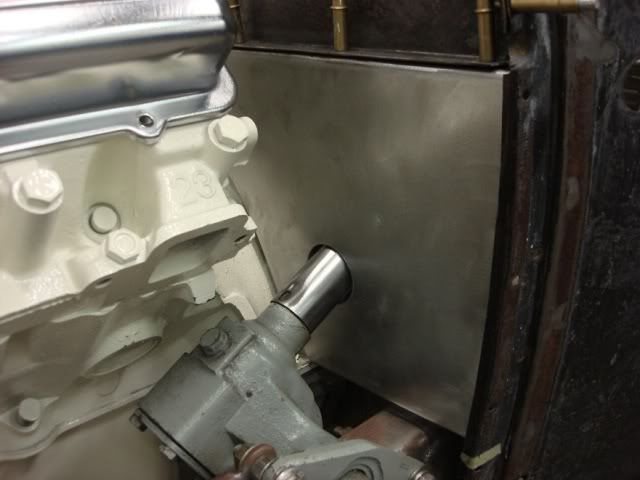
Then I had to cut another hole in the new trans hump for the American Shifter to come through. Either I am getting better at it or something, but I also hit this hole in the perfect spot the first time too. I had to grind a little more out of the hole for the shift arm to move back and forth and on the other side for the neutral safety switch clearance, but it actually came out pretty dead on.
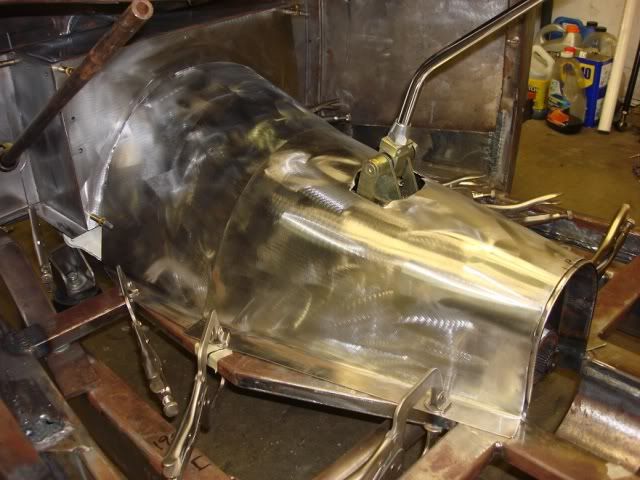
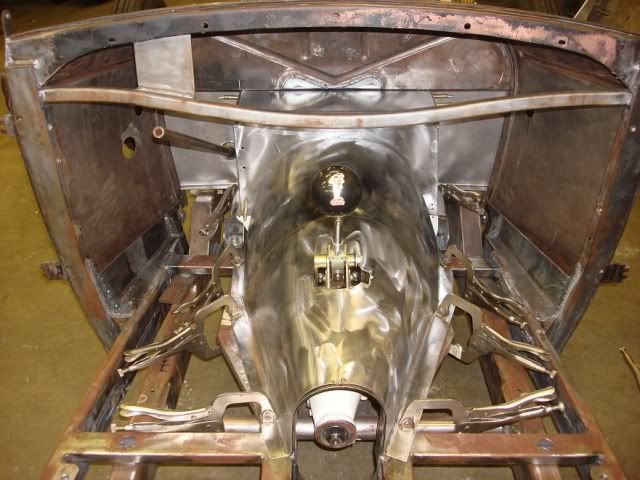
This week I am going to order a 4 x 10 foot sheet of 18 gauge sheet metal so I can finish up the floor and also start to bend up the bed. Next weekend I will get Dan to weld up all the tinwork so it is a permanent part of the subframe.
Don