donsrods
Well-known member
Thanks, Paul. Well, just for you here are some pictures . 
This is the 1/4 inch thick plate I cut to the shape of the top of the cowl. Those two tabs are just laying on it for now but will be welded on, probably tonight.
Here is the Kugel bracket bolted to the two tabs, showing how it will look when welded and installed.
This morning I ran over to the shop and drilled 5 holes around the perimeter of that plate and drilled holes in the firewall to match. Then I ran some temporary bolts through both to see how the plate fit.
Once the Kugel mount is bolted up under the dash I will make one more support bracket to tie the back part of the Kugel mount to the 1 x 1 square brace that runs under my dashboard. There is a lot of strain on the mount when you stomp on the brake pedal so I want to make it as strong as possible.
Hope this helps.
I found a couple of more pictures that might help. This was taken when my Son was building his Kugel mounts under the dash of his rpu.
This picture shows in really good detail how he did his. This is why I decided to steal his idea, it just makes such a clean installation.
Don
This is the 1/4 inch thick plate I cut to the shape of the top of the cowl. Those two tabs are just laying on it for now but will be welded on, probably tonight.
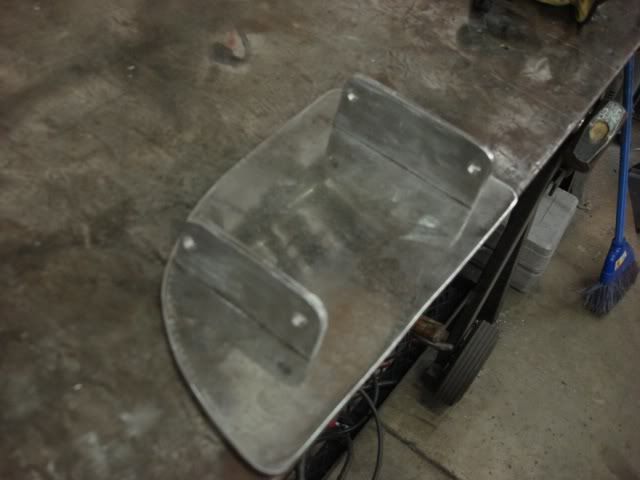
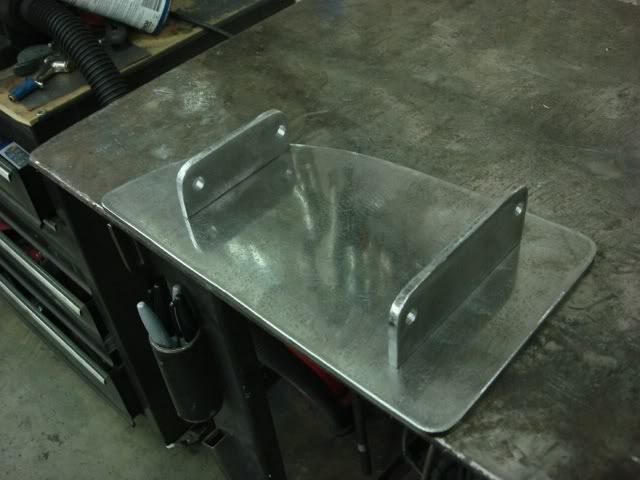
Here is the Kugel bracket bolted to the two tabs, showing how it will look when welded and installed.
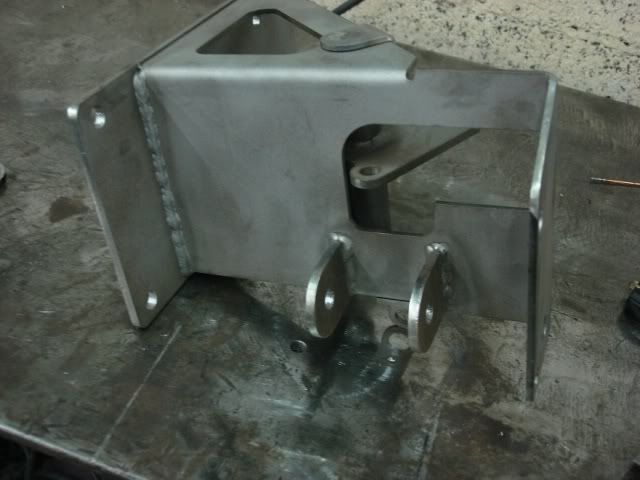
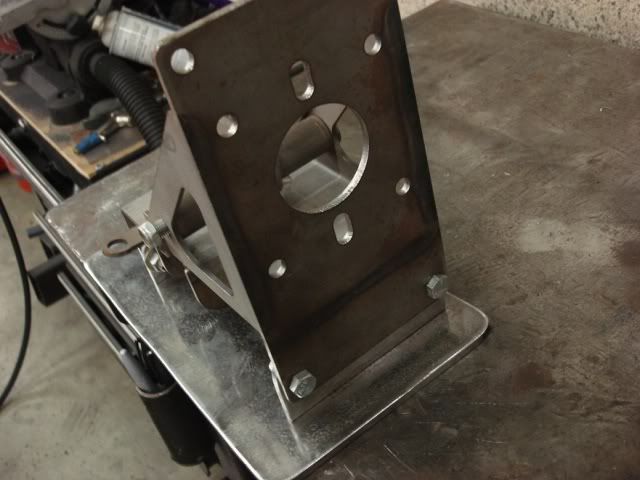
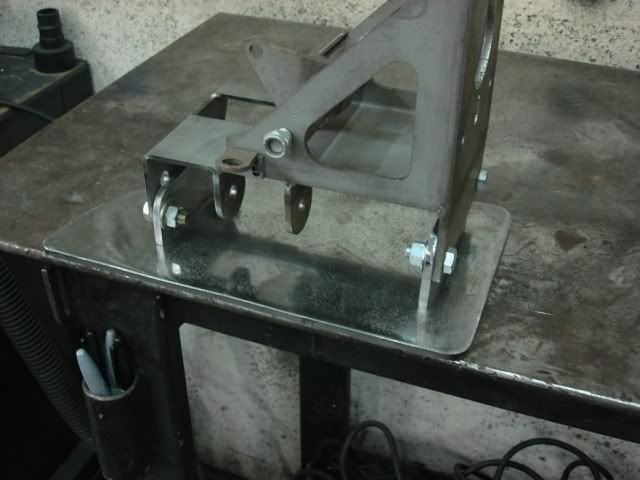
This morning I ran over to the shop and drilled 5 holes around the perimeter of that plate and drilled holes in the firewall to match. Then I ran some temporary bolts through both to see how the plate fit.
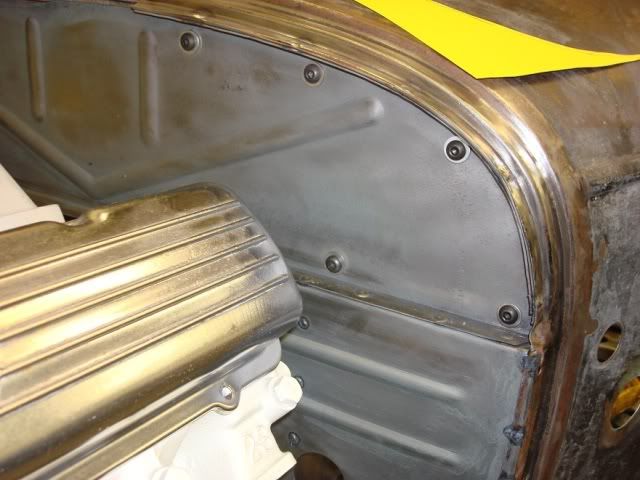
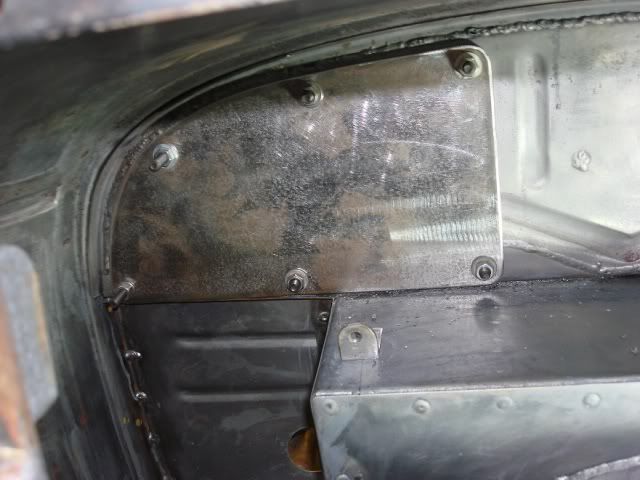
Once the Kugel mount is bolted up under the dash I will make one more support bracket to tie the back part of the Kugel mount to the 1 x 1 square brace that runs under my dashboard. There is a lot of strain on the mount when you stomp on the brake pedal so I want to make it as strong as possible.
Hope this helps.
I found a couple of more pictures that might help. This was taken when my Son was building his Kugel mounts under the dash of his rpu.

This picture shows in really good detail how he did his. This is why I decided to steal his idea, it just makes such a clean installation.
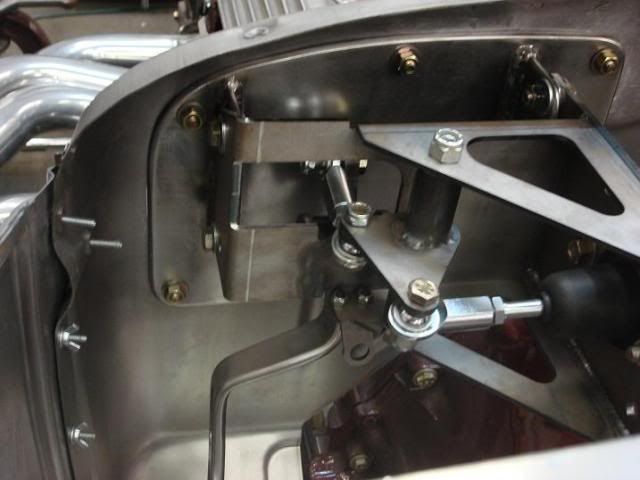
Don
Last edited: