endicott_jb
Well-known member
As far as the panhard goes, I think I can move the brackets around a bit so that it is more level. And yes the upper holes are what I had planned on using. Turns out though, I do need to at least make the brackets taller. Thank god for torches right? Lol thanks for your input. This is my first build so I'm kinda learning as I go along. I'm just trying to keep my imagination going cause my job, though I enjoy it, is a bit monotonous so I need to keep my mind working outside of work so I don't land in the looney bin again.
Version 2.1.5
Version 2.1.5
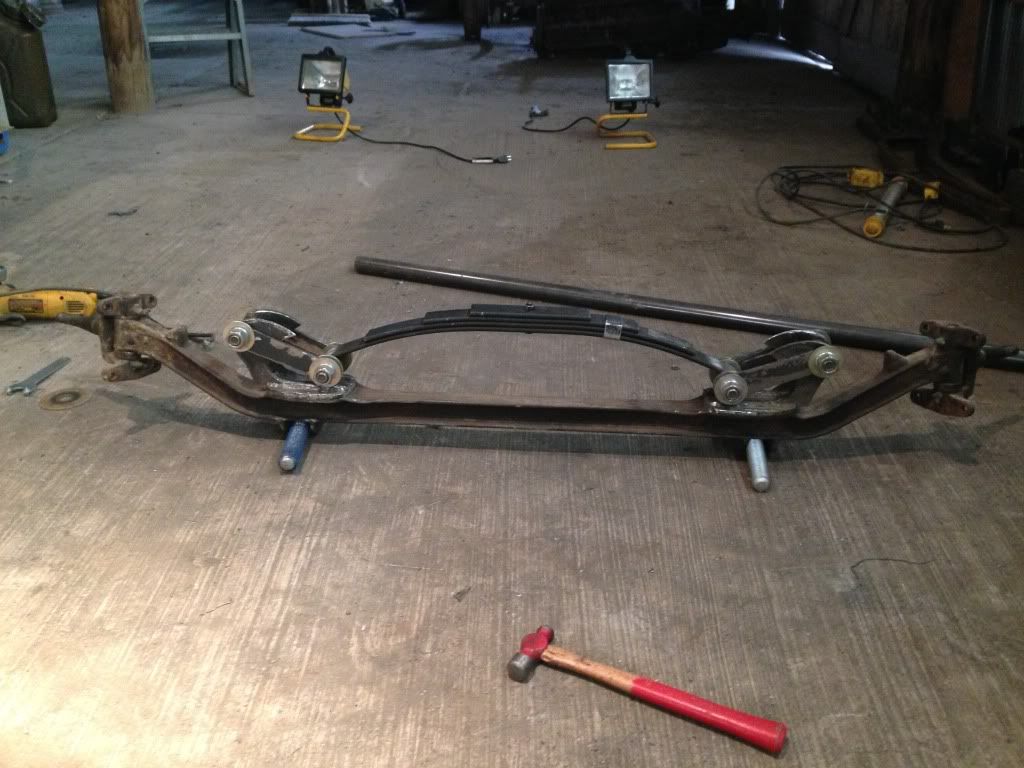